What is PFMEA, and How Can it Help You Improve Your Manufacturing Process?
- J Ross
- Nov 18, 2021
- 5 min read
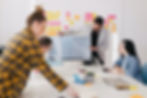
If you are a product designer or working closely with one, you probably know that a lot can go wrong if you don’t follow best practices during the design phase. Down the road, when you get into the manufacturing stage, you can end up with dimensional issues, quality problems, or component failure. And you can avoid many of these problems by adhering to the requirements of GD&T (Geometric Dimensioning and Tolerancing).
However, even after you adhere to all the necessary design standards and requirements, these issues are still likely to arise if your manufacturer does not have the right expertise, systems, and procedures in place to manufacture your product. If you want to detect and mitigate these issues, you can use a methodology called Process Failure Modes and Effects Analysis (PFMEA).
PFMEA is an essential part of the new product introduction (NPI) process, and in this article, we’ll cover the basics of the methodology. We will also present a simple PFMEA example and show you how a PFMEA can help improve your manufacturing process. By the end of this read, you’ll have enough information to perform a Process FMEA.
––––––––––––––––––––
Table of Contents:
––––––––––––––––––––
What is PFMEA?
PFMEA is a type of Failure Modes and Effects Analysis (FMEA) aimed at determining all the possible ways a manufacturing process can fail and affect the quality of the end product.
Look at it this way. During a PFMEA, you will locate and identify all human factor errors and failures associated with the methods, materials, machinery, and measurement system involved in your manufacturing process. At the end of the PFMEA, you’ll have enough information to help you mitigate the risks associated with your manufacturing process.
But how do you perform a process failure modes and effects analysis?
First, you need to determine whether your product is manufacturable before working with a cross-functional team of subject matter experts to define PFMEA. Let’s consider a simple PFMEA example.
PFMEA Example: The Painting of a Car
To help understand PFMEA, let’s consider a simple example of a car painting process using a painting machine (see Figure 1). The end goal of this painting process is to fully cover the car with the required color of paint while meeting the paint layer thickness requirement.

Figure 1. Process Failure Modes and Effects Analysis
Note: To help you better understand this PFMEA example, we’ll be presenting additional images, all of which we cropped from Figure 1. So you can always refer to Figure 1 to have the full view
PFMEA Example: Process Failure Modes and Effects
As the name suggests, process failure modes describe the ways (or manner) in which a process may fail and prevent you from getting desirable results. Column B presents the possible failure modes of the car painting process, while column C highlights the potential effects of each of the failure modes.

Figure 2. Process Failure Modes and Effects
For example, the process failure mode “foreign body in the painting layer of the car surface” will cause the car to have a poor appearance as it will keep the primer and paint from adhering. In addition, the failure mode “paint layer too thick” will likely cause the car surface to chip and crack over time.
We’ve ranked the impact of each of these potential failure modes and effects between 1 and 10 using a Severity number parameter, with 10 being the most severe and 1 having a negligible effect (See Figure 2).
PFMEA Example: More Risk Assessment with Subject Matter Experts
It’s not enough to determine the severity of each potential failure mode. If you’re going to mitigate these high risks, you will still have to:
Determine the possible causes of each of the failure modes
Rank how frequent these failures are likely to occur (see column F)
Identify the current process controls of each failure mode
Rank how likely you are to detect the failure modes with the current process controls before it affects your end products (see column H)
We’ve represented all of these processes in columns E, F, G, and H as “Potential causes,” “Occurrence,” “Current process control,” and “Detection.”

More risk assessment with subject matter experts
Note: The Occurrence and Detection columns are ranked from 1 to 10. The higher the occurrence rank, the more often the failure mode is likely to occur. In contrast, a higher detection rank translates to poorer detection capability of the current process control.
As you may have guessed, these risk assessment processes are fairly involved; it demands the expertise of a cross-functional team of subject matter experts (preferably those with at least 15 years of experience).
For example, let’s reconsider the failure mode “foreign body in the painting layer of the car surface” and assume that metal fabrication activities are ongoing in the supplier’s facility. An engineer (or specialist) might determine the cause of this failure mode to be paint contamination, usually from metal chips resulting from manufacturing processes in the facility.
The engineer will then assess the combined effect of the severity (S), occurrence (O), detection (D) ranks using a Risk Priority Number (RPN), as shown in the equation below:
Risk Priority Number (RPN) = Severity * Detection * Occurrence
Failure modes with high RPNs warrant additional review and action plans to mitigate them. For example, the failure mode “foreign body in the painting layer of the car surface” with a potential cause of “contamination of paint” has the highest RPN (288). Therefore, an additional control plan for this failure mode could be installing filtration systems in the facility to remove metal particles from the air.
Process Failure Modes and Effects Analysis: Agile in Asia Can Help
Process FMEA might seem like a process that a supplier should do on their own. But the truth is that you must be fully involved in the manufacturing process if you want to ensure your products get done right the first time.
You must ensure that your suppliers follow all the necessary rules and thoroughly assess their manufacturing process to mitigate all potential process failure modes.
Agile in Asia can help you ensure these and much more. We have a team of highly qualified engineers, manufacturing experts (covering many manufacturing processes), and supply chain experts capable of detecting and mitigating risks associated with your supplier’s facility (or your supply chain). We help businesses perform PFMEA, reducing their risks when bringing a new product to the market or working to improve their existing supply chain.
Through our PFMEA, our engineers can also provide solutions and modifications to your product design, allowing you to improve product quality and cut manufacturing costs.
Learn more about our new product introduction services.